16.07.2024
Як
Як скоротити споживання електроенергії на харчовому виробництві
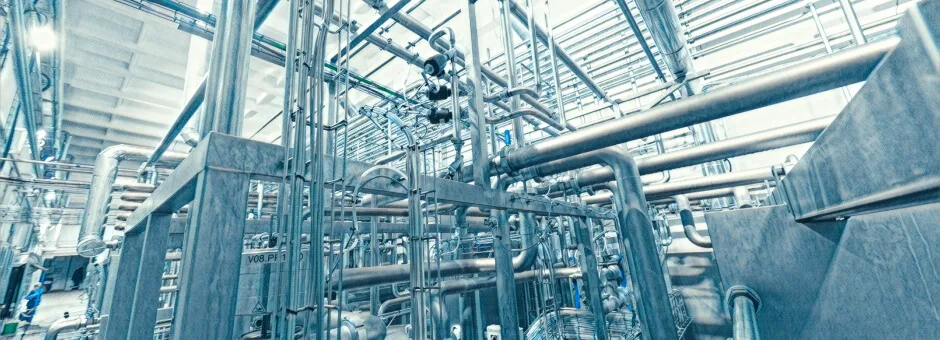
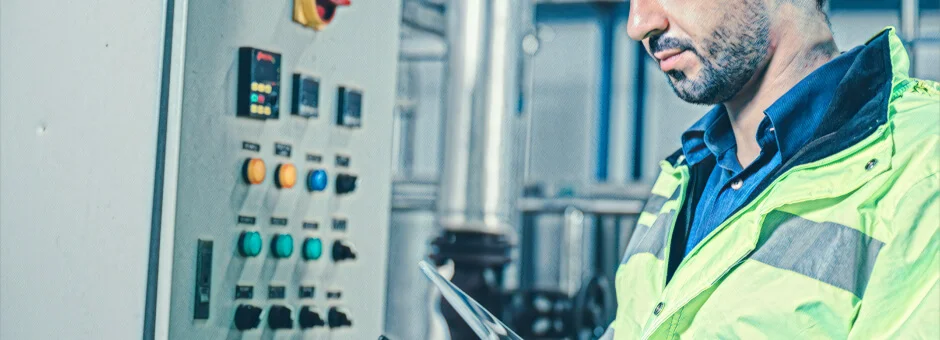
Структура основних енерговитрат на виробництві
Майже половина енергоспоживання харчового виробництва, наприклад, переробки молока, припадає на процеси очищення технологічного обладнання та трубопроводів. Але відмовитися від СІП-мийки не можна, оскільки без неї не забезпечується необхідна бактеріологічна чистота продукту.
У статті СІП-мийка на харчових виробництвах ми вже описали, яких помилок можна припустити при впровадженні обладнання та як їх уникнути.
Якщо встановити СІП станцію без зрозумілого посібника з експлуатації або з неправильним монтажем, це може призвести до серйозних проблем, включаючи гідроудари, поломки та неможливість проведення повноцінного технічного обслуговування.
Інженер-технолог, який стикається з аваріями, розбризкуванням миючого розчину та конфліктами у графіку миття різного обладнання, не оцінить переваги автоматизації, оскільки йому доведеться особисто контролювати весь процес.
Якщо миття встановлюється без урахування умов виробництва, це може спричинити проблеми і для фахівця з якості, який може зіткнутися з наявністю “мертвих зон” на лінії та неможливістю відбору проб. Щоб уникнути таких проблем, необхідно звернутись до надійної інжинірингової компанії, яка допоможе підібрати обладнання та забезпечить правильний монтаж.
Власник харчового виробництва зможе заощадити більше на мінімізації ризиків, аніж заплатить за послуги такої компанії.
Орієнтовна структура енерговитрат при CIP-процесі:
- 85 % – нагрівання мийних розчинів;
- 8 % – використання води;
- 6 % – робота електричних приводів;
- 1 % – на стиснене повітря.
Як видно, основна витрата припадає на теплові втрати, тому їхній аналіз первинний для розроблення заходів з енергозбереження.
Теплові втрати від нагрівання складаються з втрат від гарячих поверхонь ємностей і трубопроводів, від нагрітих рідин, від неправильного вибору параметрів миття – нагріву, часу, витрати води. На кожному виробництві вони індивідуальні, але є основні заходи з енергозбереження, які можна застосувати. Просто ефект у кожному випадку буде різний.
Ізоляція нагрітих поверхонь
Тепловтрати прямо пропорційні різниці температур нагрітих середовищ і навколишнього повітря. Вихід – не допускати теплообміну між гарячими поверхнями і навколишнім середовищем, щоб не було їх охолодження.
Для цього застосовується ізоляція обладнання з температурою вище 45 °С:
- ємностей;
- паропроводів і арматури;
- теплообмінників;
- трубопроводів.
У нашій практиці ізоляція бака-накопичувача паропроводу об’ємом 6 м3 приносила близько 14 євро щоденної фінансової економії. Для такої ємності потрібно 10 промивок на день за температури 85 °С. Споживання енергії при цьому становить майже 510 тис. ккал/добу.
Ізоляція корпусу, дна і кришки ємності дала змогу скоротити витрату тепла до 230 тис. ккал/добу. Витрати на дорожчий ізольований бак-накопичувач окупилися за 1,6 року. А викиди СО2 скоротилися до 20 тонн на рік. На резервуарах 20 м3 екологічний та економічний ефект буде ще помітнішим.
Теплоізоляція систем розподілу пари дає скорочення енергоспоживання на 90 %. І це обсяг прямих втрат від гарячих трубопроводів. За нашими підрахунками, теплоізоляція магістралей для гарячої води окупається за рік; труб конденсату – за 2 роки. Додатково скорочуються викиди парникових газів.
Проекти теплоізоляції гарячих поверхонь від 60 °С окупаються менше, ніж за два роки.
Скорочення втрат під час нагрівання розчину
Повторне використання мийного розчину та налаштування обладнання станції – ще один результативний захід з енергозбереження.
У багатьох процесах СІП-мийки допускається повторно використовувати рідини, але не всяка станція обладнана для цих цілей. У ній можуть бути відсутні ємності для рекуперації та поворотні магістралі від об’єктів мийки.
У результаті для кожного очищення потрібно нагрівати новий розчин до 85 °С. А використана рідина йде в дренаж.
Ще одне джерело втрат у СІП – неправильне налаштування тупикових клапанів на фліпування. Найбільший ефект від мийки досягається за їхньої пульсації в момент відкривання-закривання. А клапани залишають відкритими на 5 секунд, що збільшує витрату нагрітого розчину.
Скорочення часу нагрівання
Втрати енергії можна скоротити, знизивши температуру ємності на час приготування лужного розчину або пауз між етапами циклу мийки.
Наприклад, на 10 °С. Але тут потрібен точний розрахунок, щоб компенсувати різницю температур під час технологічного процесу.
Витрата енергії на нагрівання при зниженні на 1 °С зменшується приблизно на 1/60. Такий захід показує ефект економії пари і ресурсів у довгостроковій перспективі.
Вибір параметрів СІП-мийки
Принцип “Аналіз та оптимізація параметрів мийки під конкретні умови експлуатації” працює завжди і призводить до скорочення витрат.
СІП-процес прямо залежить від трьох складових:
- механічної – тиску і швидкості потоку;
- часу очищення;
- температури серед.
Раціональний енергоощадний підхід має на увазі збільшення механічної складової перед часом мийки та нагріванням. Наприклад, для очищення ємностей і резервуарів можна використовувати струменеві головки СІП-мийки замість щілинних. У трубопроводах збільшувати турбулентність зі швидкістю потоку не менше ніж 1,8 м/сек.
Вибір параметрів СІП-мийки завжди індивідуальний, оскільки він залежить від типу забруднень, виду продукту, конструктивних особливостей обладнання та трубопроводів. Знайти найкращий варіант для вашого виробництва можна після проведення тестів і лабораторних змивів.
Приклад. На підприємствах переробки молока хороший енергозберігаючий ефект дає підбір температури очищення обладнання.
Повторне використання питної води
Це цінний ресурс, оскільки його виробництво також енерговитратне.
Дбайливо витрачати питну воду можна за допомогою її повторного використання. Так рідину від останнього ополіскування під час СІП-мийки застосовують для першого промивання в наступному циклі.
Для того, щоб це реалізувати, потрібна модернізація наявної станції зі встановленням рекупераційного обладнання: ємностей і трубопроводів.
Скорочення втрат від насосів
Найефективнішим заходом зниження електричних втрат є встановлення частотних перетворювачів з контролем витрати і тиску.
Це пристрої, які змінюють частоту змінного струму основної мережі до потрібних параметрів, що дає змогу регулювати швидкість електродвигуна насоса відповідно до потреб технологічного процесу.
Встановлення частотника належить до модернізації електроустановки. Проектування і виконання цієї роботи краще доручити інжиніринговій фірмі, щоб не отримувати претензії від мережевої компанії та органів енергонагляду. Річ у тім, що частотні перетворювачі можуть погіршувати якість електроенергії в основній мережі.
Обслуговування та підтримання технічного стану обладнання
Обладнання в поганому стані обходиться власнику дорожче.
Обладнання в поганому стані обходиться власнику дорожче. Негерметичні ущільнення, забиті мийні головки і зношені насоси сильно збільшують втрати пари, води, електрики. Протікання зведуть “на нуль” ефект від реалізації інших енергозберігаючих заходів.
Тому своєчасне технічне обслуговування, ремонт і заміна застарілого обладнання – одна з умов раціонального теплоспоживання. Наведемо як приклад конденсатовідвідники.
Якщо їхнє техобслуговування не проводилося 3-5 років, то приблизно третина такого обладнання перебуває в несправному стані, даючи змогу парі просочуватися в систему відведення. Такі показники підтверджуються практикою.
Щоб скоротити витрати на ремонт і заміну, харчові підприємства застосовують систему віддаленого моніторингу. Це варіація промислового інтернету речей – Industrial Internet of Things або IIoT. Спеціальні датчики збирають інформацію про параметри роботи різного устаткування і передають їх у систему управління. Такий моніторинг допомагає витрачати кошти на ремонт і заміну саме непрацюючого обладнання. З нашого досвіду на харчових підприємствах із системою моніторингу несправно не більше 5 % конденсатовідвідників, а втрати пари зменшуються на 10 %.
Сучасні моделі обладнання більш енергоефективні, ніж випущені десятки років тому. Наприклад, зараз термостатичні конденсатовідвідники мають низку переваг перед старими моделями:
- вони відкриваються, коли температура наближається до рівня насиченої пари плюс-мінус два градуси;
- можуть використовуватися як повітропроводи;
- викидають неконденсовані гази після кожного відкриття;
- зменшують час на нагрівання
Середній термін окупності заміни конденсатовідвідника становить менше шести місяців.
Замість висновку
На ефективність роботи та енергоспоживання харчового обладнання впливають:
- правильне розташування елементів парової температури;
- коефіцієнт теплопередачі;
- матеріал і тип теплообмінника;
- продуктивність теплообмінника;
- наявність витоків.