05.09.2024
How
Study
5 Key Design aspects for CIP system
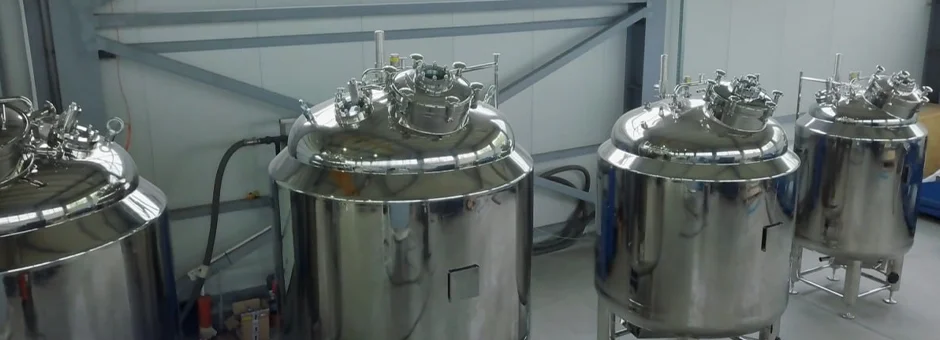
A Clean-in-Place (CIP) system is an efficient and cost-effective solution for cleaning the internal surfaces of food processing equipment and piping without the need for disassembly. A well-designed CIP system not only enhances sanitation and food safety but also simplifies cleaning procedures for operators, by reducing downtime. By automating what was once a time-consuming manual process of dismantling, hand-cleaning, and reassembling equipment, a CIP system ensures thorough cleaning while optimizing production efficiency.
When considering investing in a CIP system, it’s crucial to prioritize a design that is reliable and up-to-date. Your request to the CIP station supplier should include the specific needs of your facility, including factors such as the number of washing objects, their features and specifics, number of CIP supply lines, switching efficiency, water and chemical savings and system complexity and design.
In addition to the financial losses incurred from halted production, inadequately cleaned equipment can pose serious risks by spreading foodborne contaminants between batches, endangering consumers, and potentially triggering damaging recalls that impact a company’s bottom line and reputation.
For a CIP system to be effective, equipment and piping must be designed for easy cleaning and installed according to hygienic standards. This entails ensuring free draining piping, eliminating “dead legs,” and ensuring that the water used for the final rinse meets product contact specifications.
Key Design aspects:
1. Understand what exactly needs to be cleaned and how:
Tailor your CIP system design to your facility’s specific cleaning requirements. Consider factors such as cleaning frequency, types of fouling, and any unique sanitation requirements.
2. CIP process and production schedule:
Consider the size of the CIP system needed and its impact on production schedules. Account for variables such as the number of circuits to be cleaned simultaneously, cleaning frequency, required flow rates, and types of chemicals needed.
3. Cleaning solution compatibility:
Select cleaning solutions and components or pipe materials that are compatible to avoid damage to equipment. Consider upgrading piping or elastomers if harsh cleaning solutions are necessary, and plan for compatibility from the outset of system development.
4. Reduce water and chemical consumption:
Implement water-saving techniques and alternative chemical treatments to minimize water and chemical usage. Explore methods such as product recovery, pigging, and air blows to reduce rinsing times and conserve resources.
5. Flow rate and pressure:
The CIP system must be able to maintain the correct flow rate and pressure, especially when cleaning multiple circuits simultaneously. Properly size drain valves and pipe routing to prevent flooding and ensure operator safety.