16.07.2024
How
How to reduce electricity consumption in food production
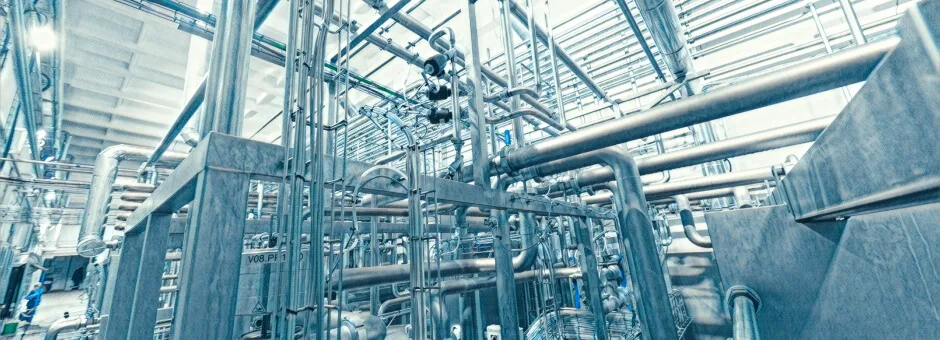
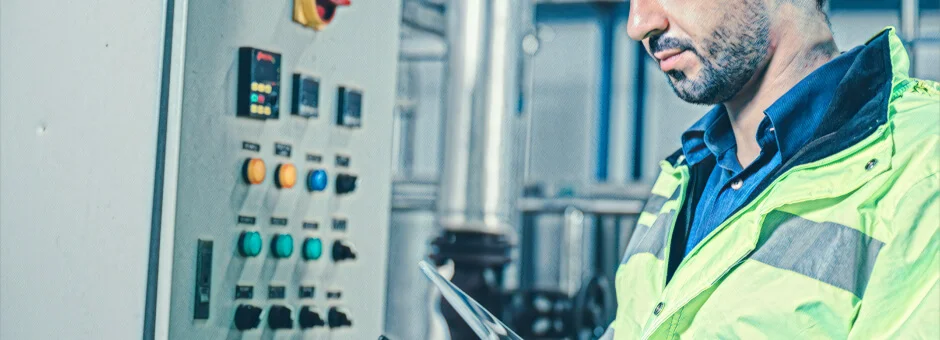
Structure of the main energy costs in production
Almost half of the energy consumption of food production, such as milk processing, is accounted for by the cleaning of process equipment and pipelines. However, it is impossible to refuse to use SIP washing, as it does not ensure the necessary bacteriological purity of the product.
In the article CIP washing in food production, we have already described what mistakes can be made when implementing the equipment and how to avoid them.
If you install a SIP station without a clear operating manual or with an incorrect installation, it can lead to serious problems, including water hammer, breakdowns, and the inability to perform proper maintenance.
A process engineer who faces accidents, splashing of cleaning solution, and conflicts in the washing schedule of different equipment will not appreciate the benefits of automation, as he or she will have to personally control the entire process.
If washing is installed without taking into account the production conditions, this can also cause problems for the quality specialist, who may face the presence of “dead zones” on the line and the inability to take samples. To avoid such problems, it is necessary to contact a reliable engineering company that will help you select the equipment and ensure proper installation.
The owner of a food production facility will be able to save more on minimizing risks than he or she will pay for the services of such a company.
Approximate structure of energy consumption in the CIP process:
The first step in selecting technical solutions is to find energy leaks. For this purpose, remote monitoring systems consisting of detectors and software can be used. Sensors are installed on the process equipment, and the process parameters are recorded over a certain period of time.
- 85% – heating of cleaning solutions;
- 8% – water consumption;
- 6% – operation of electric drives;
- 1% – compressed air.
As you can see, heat losses account for the main consumption, so their analysis is primary for developing energy saving measures.
Heat losses from heating consist of losses from hot surfaces of containers and pipelines, from heated liquids, from the wrong choice of washing parameters – heating, time, water consumption. They are individual for each production facility, but there are basic energy saving measures that can be applied. The effect will be different in each case.
Insulation of heated surfaces
Heat loss is directly proportional to the temperature difference between the heated media and the ambient air. The solution is to prevent heat exchange between hot surfaces and the environment so that they do not cool down.
For this purpose, insulation of equipment with a temperature above 45 °C is used:
- tanks
- steam lines and fittings;
- heat exchangers;
- pipelines.
In our practice, the insulation of a 6 m3 steam pipeline storage tank brought about 14 euros in daily financial savings. Such a tank requires 10 flushes per day at a temperature of 85 °C. The energy consumption is almost 510 thousand kcal/day.
Insulation of the tank body, bottom, and lid reduced heat consumption to 230 thousand kcal/day. The cost of a more expensive insulated storage tank was paid off in 1.6 years. And CO2 emissions were reduced to 20 tons per year. With 20 m3 tanks, the environmental and economic effect will be even more noticeable.
Thermal insulation of steam distribution systems reduces energy consumption by 90%. And this is the amount of direct losses from hot pipelines. According to our estimates, the insulation of hot water lines pays for itself in a year; condensate pipes – in 2 years. In addition, greenhouse gas emissions are reduced.
Projects for thermal insulation of hot surfaces above 60 °C pay off in less than two years.
Reduced losses during solution heating
Reusing the cleaning solution and adjusting the plant’s equipment is another effective energy saving measure.
Many CIP washing processes allow for the reuse of fluids, but not every station is equipped for this purpose. It may not have recovery tanks or return lines from the wash objects.
As a result, a new solution needs to be heated to 85°C for each cleaning. And the used liquid goes into drainage.
Another source of losses in the SIP is the incorrect setting of dead-end valves for flip-flopping. The greatest effect of washing is achieved when they pulsate when opening and closing. And the valves are left open for 5 seconds, which increases the flow of heated solution.
Reduced heating time
Energy losses can be reduced by lowering the temperature of the vessel during the preparation of the alkaline solution or pauses between the stages of the cleaning cycle.
For example, by 10°C. But this requires an accurate calculation to compensate for temperature differences during the process.
The energy consumption for heating is reduced by about 1/60 of the total by 1 °C. This measure shows the effect of saving steam and resources in the long term.
Selecting the parameters of the SIP sink
The principle of “Analyzing and optimizing washing parameters for specific operating conditions” always works and leads to cost savings.
The CIP process directly depends on three components:
- mechanical – pressure and flow rate;
- cleaning time;
- temperature of the medium.
A rational energy-saving approach involves increasing the mechanical component before the cleaning time and heating. For example, to clean tanks and reservoirs, you can use jet heads of a CIP washer instead of slot heads. In pipelines, increase turbulence with a flow rate of at least 1.8 m/sec.
The choice of SIP washing parameters is always individual, as it depends on the type of contaminants, the type of product, and the design features of the equipment and pipelines. You can find the best option for your production after conducting tests and laboratory flushes.
Example. At milk processing plants, a good energy-saving effect is achieved by selecting the cleaning temperature of the equipment.
Reuse of drinking water
This is a valuable resource because its production is also energy-intensive.
You can conserve drinking water by reusing it. For example, the liquid from the last rinse during the CIP wash is used for the first rinse in the next cycle.
In order to implement this, the existing station needs to be modernized with the installation of recovery equipment: tanks and pipelines.
Reducing losses from pumps
The most effective measure to reduce electrical losses is to install frequency converters with flow and pressure control.
These are devices that change the alternating current frequency of the main network to the required parameters, which makes it possible to adjust the speed of the pump motor in accordance with the needs of the technological process.
Installing a frequency converter is a modernization of the electrical installation. It is better to entrust the design and implementation of this work to an engineering firm to avoid receiving complaints from the grid company and energy supervisors. The fact is that frequency converters can deteriorate the quality of electricity in the main grid.
Maintenance and support of the technical condition of the equipment
Equipment in poor condition is more expensive for the owner.
Equipment in poor condition is more expensive for the owner. Leaky seals, clogged wash heads, and worn-out pumps greatly increase the loss of steam, water, and electricity. Leaks will reduce the effect of other energy-saving measures to zero.
Therefore, timely maintenance, repair and replacement of outdated equipment is one of the conditions for rational heat consumption. Let’s take condensate traps as an example.
If they have not been serviced for 3-5 years, then about a third of such equipment is in a faulty condition, allowing steam to leak into the drainage system. These figures are confirmed by practice.
To reduce the cost of repairs and replacements, food companies use a remote monitoring system. This is a variation of the Industrial Internet of Things (IIoT). Special sensors collect information about the operating parameters of various equipment and transmit it to the control system. Such monitoring helps to spend money on repairing and replacing the equipment that is not working. According to our experience, no more than 5% of condensate traps are malfunctioning at food processing plants with a monitoring system, and steam losses are reduced by 10%.
Modern equipment models are more energy efficient than those produced decades ago. For example, thermostatic steam traps now have a number of advantages over older models:
- They open when the temperature approaches the level of saturated steam plus or minus two degrees;
- can be used as air ducts;
- emit non-condensed gases after each opening;
- reduce heating time
The average payback period for replacing a steam trap is less than six months.
Instead of a conclusion
The efficiency and energy consumption of food processing equipment are affected:
- correct arrangement of steam temperature elements;
- heat transfer coefficient;
- material and type of heat exchanger;
- heat exchanger performance;
- presence of leaks.