03.09.2024
How
Study
Cleaning of small tanks
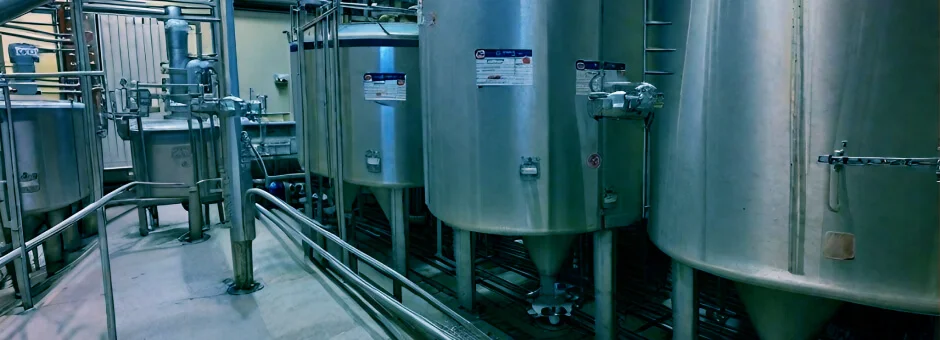
Small vessels are used in a variety of industries including brewing, dairy, confectionery, pharmaceuticals, and wherever low volume production is required.
These vessels can be categorised as follows:
- Small vessels: up to 500 litres.
- Medium-sized vessels: between 500 litres and 5 cubic metres.
- Large vessels: over 5 cubic metres.
How are small tanks cleaned?
The cleaning of small tanks is not usually limited to one method. There are different approaches:
Manual cleaning
This method involves opening the tank, washing it manually and closing it. However, in terms of microbiological cleanliness, this method is not always effective and involves risks to the product and hygiene.
Automatic washing
This method involves the use of special washing nozzles inside the container. Depending on the type of washing, these may be:
- Static washing nozzle, which delivers cleaning solution or pressurised water in specific directions.
- Rotary wash nozzle, which rotates when the cleaning solution is delivered, providing a more effective mechanical action.
- Directional nozzles, which also rotate and are able to deliver a larger volume of cleaning fluid, providing a more intense mechanical action on the vessel walls.
The four factors of the CIP system
The self-cleaning system (CIP) includes four factors that affect the washing process:
- Temperature factor: The temperature of the cleaning solution affects the quality of the wash.
- Chemical factor: The concentration of the cleaning solution plays a role in the cleaning efficiency.
- Mechanical factor: Mechanical action, as the moment of washing, is important to remove contaminants.
- Time factor: The time taken for washing is also important.
By varying these factors, the quality of the wash can be optimised. For example, an increase in mechanical action can compensate for a decrease in other factors such as temperature, cleaning solution concentration and washing time.
Features of washing small containers
An important aspect of washing small vessels is to efficiently flow the cleaning solution down the sides and avoid trapping it inside the vessel. This ensures mechanical action on the entire surface. For this purpose, it is important to maintain a minimum level of cleaning solution inside the tank to prevent stagnation.
The selection of the pump for pumping out the cleaning solution is also important to avoid possible problems with blockages. Different types of pumps may have different sensitivities to fluid delivery and air locks, which must be taken into account when selecting equipment.
Overall, washing small tanks requires attention to detail and process optimisation to ensure that contaminants are removed effectively and hygiene standards are met across a wide range of industries.
In the case of small vessels, maintaining a balance between supplying and pumping the cleaning solution is a key challenge. It is necessary to avoid overfilling the vessel and at the same time provide sufficient mechanical action on the contaminants. Overcoming this difficulty requires the following approaches:
- Detergent level: Monitor the level of detergent inside the tank. To do this, use level sensors that can control the pump to maintain the optimum liquid level. Select sensors that work reliably even in humid conditions.
- Prevent swirling: If the supply and pumping of the cleaning solution is done from below, pay attention to the possible formation of a funnel. Design solutions such as cross ribs can be implemented to prevent funneling.
- Additional heads: If there are agitators or other obstructions inside the tank, consider installing additional wash heads that provide mechanical action to all areas, including the bottom of the agitator blades.
- Monitoring Systems: It is important to implement monitoring systems to help track wash parameters to ensure process quality and identify problems. This can include monitoring temperature, solution concentration, and other important parameters.
- Automation: The more automated the washing process is, the less reliance on human intervention. Try to automate the CIP system as much as possible to minimise risks and ensure consistent wash quality.
- Selecting a CIP system: The approach to selecting a CIP system depends on the specific application. Consider the type of tanks, the degree of soiling, the need for different wash heads, detergent concentrations and other factors to find the best system for each application.
- Wash head efficiency: Consider the different types of wash heads, such as static and rotary. Rotary heads are often more efficient due to their ability to provide more uniform and intense mechanical action.
- Rotary head monitoring: If rotary heads are used, choose models with rotation sensors that allow you to monitor and control the condition of the equipment.
Overall, an effective CIP system for small vessels requires careful planning, automation and monitoring to ensure optimum wash quality and minimise risks.