- Home
- Mini CIP station
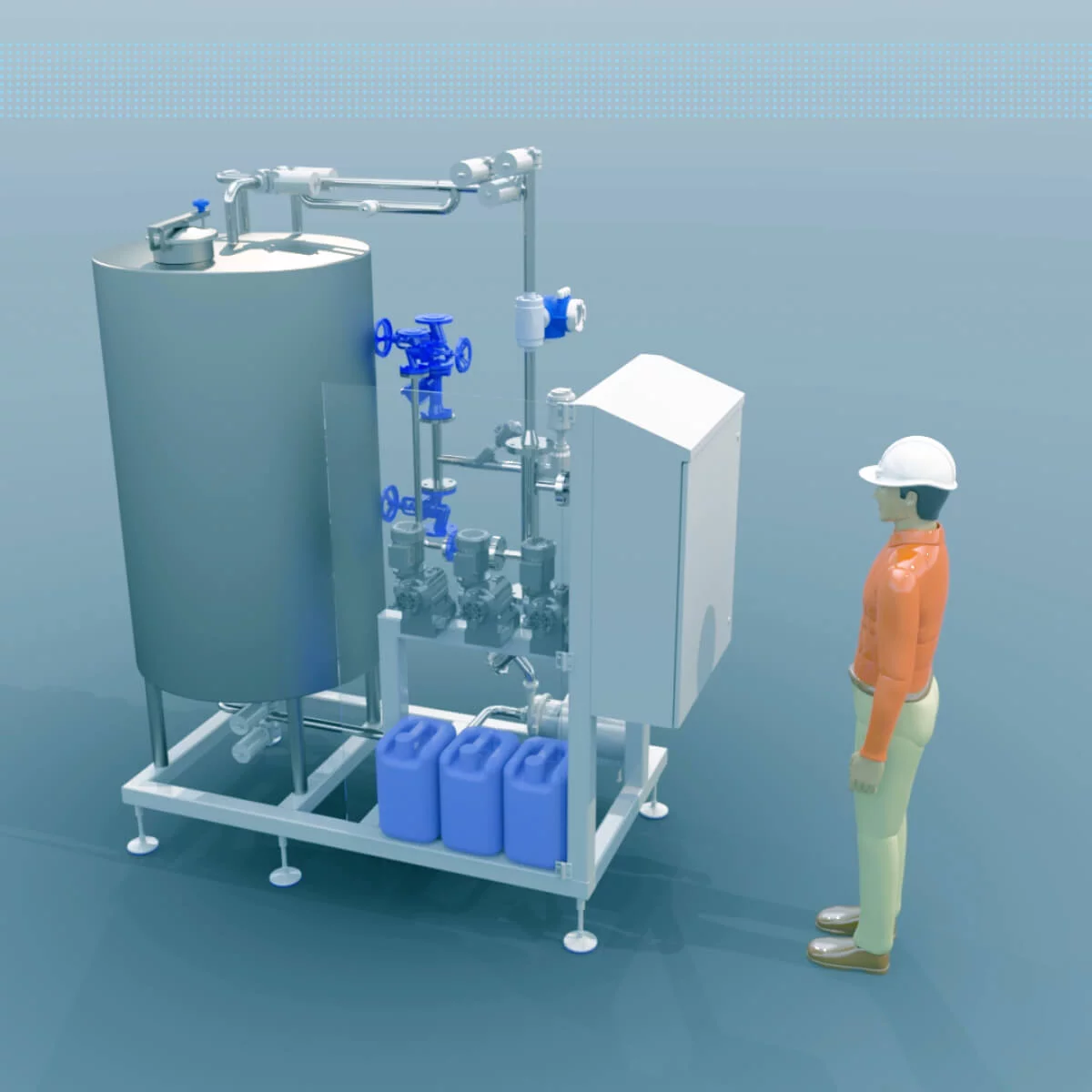
Mini CIP station
The automatic mini-CIP station by VIRAVIX is designed to ensure efficient and precise cleaning of plants. This unit is designed to facilitate the removal of contaminants and reduce bacteria levels, guaranteeing safety and high product quality.
Contact USIntroduction & Application
VIRAVIX offers a mini-CIP station unit for plants, where a sufficient level of automation is necessary, to facilitate the cleaning of these plants, to remove the impurities and to reduce bacterial presence. Also, this is why, when thinking about small facilities that require a certain level of automation, VIRAVIX designed an automatic CIP system to help to clean plants, eliminate impurities, and reduce bacteria levels.
Hygiene is an essential factor in the food processing, cosmetics and pharmaceutical industries. Cleaning in Place is considered another stage of the production process. In the foodprocessing industry a defective cleaning causes contamination of the product and affects its quality, also incorrect cleaning in the food industry can lead to the loss of an entire day’s production and directly affect the end product’s quality.
Structural Framing
- Design: Closed square/round tubing
- Surface Finish: Bead blasted
- Material: 304 square/round tubing
- Fully welded single piece construction.
Sanitary Piping
- Material: 304/316 sanitary tube and fittings
- Surface Finish: 0.8Ra
- Valves: Butterfly type, 304/316 body, EPDM and manual/electric/air/ actuator
Buffer tanks
- Volume: 1000-3000l
- Interior and exterior finish: 0.8 Ra with weld color removed frame
- Tank sidewall insulation: no/yes with 304 sheathing
- Material: AISI304 or AISI316
- The tank(s) are mounted to the CIP station frame
Local Chemical Addition
There are two (2) options for adding local chemical addition to the skid:
- Local Chemical Pump Assembly & (1) Chemical Reservoir with Low-Level Switch
- Local Chemical Pump Assemblies & (2) Chemical Reservoirs with Low-Level Switches
The chemical pump assembly doses the cleaning chemicals and/or sanitizer from a storage drum to the injection point on the CIP system. The concentrations are controlled to a time based setpoint value or to a conductivity setpoint value if the Conductivity Monitoring/Control option is chosen. The chemical pump assembly(s) are mounted to the CIP frame.
Chemical Reservoirs with Low-Level Switches – the reservoir provides an on-skid location to store chemical for use in the cleaning cycle. Quick disconnects make the reservoir easy to remove for filling. A level switch is integral to the assembly, providing a low-level alarm.
Heating System
Steam/Hot water heating method is provided. The system will wash the target equipment using water after preheating.
- Heat Exchanger – Steam/Hot water
- The Heat Exchanger – Steam/Hot water, a shell & tube or PHE heat exchanger provides indirect heating of the wash solutions. The heat exchanger will be located in the discharge of the supply pump.
Control System
The electrical cabinet and components used to control the system are skid mounted.
- Schneider/Allen-Bradley/Siemens/Delta’s PLC with associated digital and analog outputs
- Frequency converter (for CIP Supply pump)
Operator interfaces can include the HMI and other components installed on the control panel.
- Schneider/Allen-Bradley/Siemens/Weintek/Delta with color 7”,9” touchscreen, Operator Terminal (HMI)
- Illuminated emergency stop/reset/LOTO switches
Reporting & Remote access
- QVisor- Data Acquisition & Management System
- TeamViewer IoT – Online Data Acquisition & Management System
Cleaning Cycles
The following phases are an example of a typical CIP cycle. Water fill, water drain, chemical addition, and/or heating steps are not listed but can be part of the phases. All cleaning steps are setup as individual operation codes enabling full customization of cleaning cycles.
- Pre-Rinse
- Rinse
- Caustic Wash
- Final Rinse (With or Without Sanitizer)
- Acid Wash
System Automation Programming of the HMI and PLC provide automation of the system.
- Cleaning sequences will be automatically controlled through the use of cleaning cycle recipes.
- Each recipe has its own setpoint values (e.g., time, temperature, conductivity, flow) which are adjustable
- Measured process variables have alarms with adjustable high/low setpoint values
Benefits & Advantages
The mini- CIP station by VIRAVIX has been designed according to “good practice” steps, easy maintenance, high quality and versatility in mind. Touch screen options , the program with built-in clean cycles, PLC interface to control pump speed and consumption , chemical concentration and temperature for consistent results. By automating the cleaning procedure with a mini CIP, a plant can reduce cleaning time, reduce downtime, and increase repeatability through process parameters.
Structural Framing
- Design: Closed square/round tubing
- Surface Finish: Bead blasted
- Material: 304 square/round tubing
- Fully welded single piece construction.
Sanitary Piping
- Material: 304/316 sanitary tube and fittings
- Surface Finish: 0.8Ra
- Valves: Butterfly type, 304/316 body, EPDM and manual/electric/air/ actuator
Buffer tanks
- Volume: 1000-3000l
- Interior and exterior finish: 0.8 Ra with weld color removed frame
- Tank sidewall insulation: no/yes with 304 sheathing
- Material: AISI304 or AISI316
- The tank(s) are mounted to the CIP station frame
Local Chemical Addition
There are two (2) options for adding local chemical addition to the skid:
- Local Chemical Pump Assembly & (1) Chemical Reservoir with Low-Level Switch
- Local Chemical Pump Assemblies & (2) Chemical Reservoirs with Low-Level Switches
The chemical pump assembly doses the cleaning chemicals and/or sanitizer from a storage drum to the injection point on the CIP system. The concentrations are controlled to a time based setpoint value or to a conductivity setpoint value if the Conductivity Monitoring/Control option is chosen. The chemical pump assembly(s) are mounted to the CIP frame.
Chemical Reservoirs with Low-Level Switches – the reservoir provides an on-skid location to store chemical for use in the cleaning cycle. Quick disconnects make the reservoir easy to remove for filling. A level switch is integral to the assembly, providing a low-level alarm.
Heating System
Steam/Hot water heating method is provided. The system will wash the target equipment using water after preheating.
- Heat Exchanger – Steam/Hot water
- The Heat Exchanger – Steam/Hot water, a shell & tube or PHE heat exchanger provides indirect heating of the wash solutions. The heat exchanger will be located in the discharge of the supply pump.
Control System
The electrical cabinet and components used to control the system are skid mounted.
- Schneider/Allen-Bradley/Siemens/Delta’s PLC with associated digital and analog outputs
- Frequency converter (for CIP Supply pump)
Operator interfaces can include the HMI and other components installed on the control panel.
- Schneider/Allen-Bradley/Siemens/Weintek/Delta with color 7”,9” touchscreen, Operator Terminal (HMI)
- Illuminated emergency stop/reset/LOTO switches
Reporting & Remote access
- QVisor- Data Acquisition & Management System
- TeamViewer IoT – Online Data Acquisition & Management System
Cleaning Cycles
The following phases are an example of a typical CIP cycle. Water fill, water drain, chemical addition, and/or heating steps are not listed but can be part of the phases. All cleaning steps are setup as individual operation codes enabling full customization of cleaning cycles.
- Pre-Rinse
- Rinse
- Caustic Wash
- Final Rinse (With or Without Sanitizer)
- Acid Wash
System Automation Programming of the HMI and PLC provide automation of the system.
- Cleaning sequences will be automatically controlled through the use of cleaning cycle recipes.
- Each recipe has its own setpoint values (e.g., time, temperature, conductivity, flow) which are adjustable
- Measured process variables have alarms with adjustable high/low setpoint values
Design
Technical information provided within this document is for VIRAVIX ’s c onfigured d esign o ffering of the mini CIP – a skid mounted , compact – 1 or 2 tank s Clean-In-Place (CIP) system by VIRAVIX designed for the food, beverage, personal care, or nutraceutical industries. Alternative d esign r equests for variations in construction, size, component manufacturers, options, orientation, or other technical requirements should be directed to a VIRAVIX representative or a sales channel for custom quoting and engineering.
Structural Framing
- Design: Closed square/round tubing
- Surface Finish: Bead blasted
- Material: 304 square/round tubing
- Fully welded single piece construction.
Sanitary Piping
- Material: 304/316 sanitary tube and fittings
- Surface Finish: 0.8Ra
- Valves: Butterfly type, 304/316 body, EPDM and manual/electric/air/ actuator
Buffer tanks
- Volume: 1000-3000l
- Interior and exterior finish: 0.8 Ra with weld color removed frame
- Tank sidewall insulation: no/yes with 304 sheathing
- Material: AISI304 or AISI316
- The tank(s) are mounted to the CIP station frame
Local Chemical Addition
There are two (2) options for adding local chemical addition to the skid:
- Local Chemical Pump Assembly & (1) Chemical Reservoir with Low-Level Switch
- Local Chemical Pump Assemblies & (2) Chemical Reservoirs with Low-Level Switches
The chemical pump assembly doses the cleaning chemicals and/or sanitizer from a storage drum to the injection point on the CIP system. The concentrations are controlled to a time based setpoint value or to a conductivity setpoint value if the Conductivity Monitoring/Control option is chosen. The chemical pump assembly(s) are mounted to the CIP frame.
Chemical Reservoirs with Low-Level Switches – the reservoir provides an on-skid location to store chemical for use in the cleaning cycle. Quick disconnects make the reservoir easy to remove for filling. A level switch is integral to the assembly, providing a low-level alarm.
Heating System
Steam/Hot water heating method is provided. The system will wash the target equipment using water after preheating.
- Heat Exchanger – Steam/Hot water
- The Heat Exchanger – Steam/Hot water, a shell & tube or PHE heat exchanger provides indirect heating of the wash solutions. The heat exchanger will be located in the discharge of the supply pump.
Control System
The electrical cabinet and components used to control the system are skid mounted.
- Schneider/Allen-Bradley/Siemens/Delta’s PLC with associated digital and analog outputs
- Frequency converter (for CIP Supply pump)
Operator interfaces can include the HMI and other components installed on the control panel.
- Schneider/Allen-Bradley/Siemens/Weintek/Delta with color 7”,9” touchscreen, Operator Terminal (HMI)
- Illuminated emergency stop/reset/LOTO switches
Reporting & Remote access
- QVisor- Data Acquisition & Management System
- TeamViewer IoT – Online Data Acquisition & Management System
Cleaning Cycles
The following phases are an example of a typical CIP cycle. Water fill, water drain, chemical addition, and/or heating steps are not listed but can be part of the phases. All cleaning steps are setup as individual operation codes enabling full customization of cleaning cycles.
- Pre-Rinse
- Rinse
- Caustic Wash
- Final Rinse (With or Without Sanitizer)
- Acid Wash
System Automation Programming of the HMI and PLC provide automation of the system.
- Cleaning sequences will be automatically controlled through the use of cleaning cycle recipes.
- Each recipe has its own setpoint values (e.g., time, temperature, conductivity, flow) which are adjustable
- Measured process variables have alarms with adjustable high/low setpoint values