16.07.2024
Jak
Jak zmniejszyć zużycie energii elektrycznej w produkcji żywności
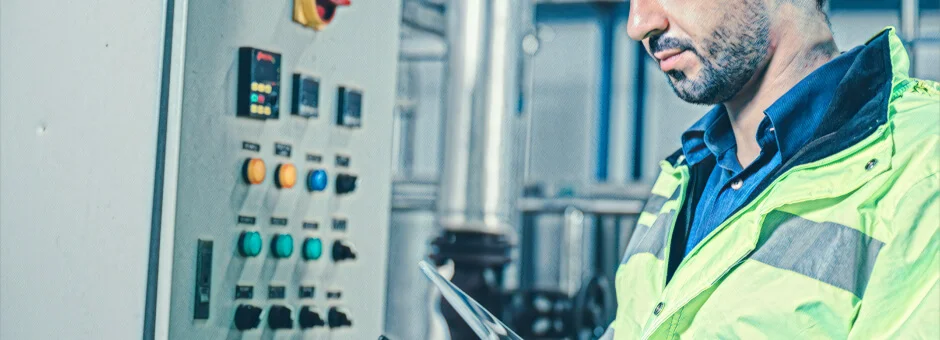
Struktura głównego zużycia energii w produkcji
Prawie połowa zużycia energii w produkcji żywności, takiej jak przetwórstwo mleka, przypada na czyszczenie urządzeń procesowych i rurociągów. Nie można jednak zrezygnować z mycia SIP, ponieważ nie zapewnia ono wymaganej czystości bakteriologicznej produktu.
W artykule Mycie w obiegu zamkniętym CIP w produkcji żywności opisaliśmy już, jakie błędy można popełnić podczas wdrażania sprzętu i jak ich uniknąć.
Instalacja stacji CIP bez jasnej instrukcji obsługi lub z nieprawidłową instalacją może prowadzić do poważnych problemów, w tym uderzeń wodnych, awarii i niemożności przeprowadzenia właściwej konserwacji.
Inżynier procesu, który ma do czynienia z wypadkami, rozpryskiwaniem roztworu czyszczącego i konfliktami w harmonogramie mycia różnych urządzeń, nie doceni korzyści płynących z automatyzacji, ponieważ będzie musiał osobiście kontrolować cały proces.
Jeśli mycie jest instalowane bez uwzględnienia warunków produkcji, może to również powodować problemy dla specjalisty ds. jakości, który może napotkać martwe punkty na linii i niemożność pobrania próbek. Aby uniknąć takich problemów, konieczne jest skontaktowanie się z niezawodną firmą inżynieryjną, która pomoże wybrać sprzęt i zapewni prawidłową instalację.
Właściciel zakładu produkującego żywność będzie w stanie zaoszczędzić więcej na minimalizacji ryzyka, niż zapłaci za usługi takiej firmy.
Przybliżona struktura zużycia energii w procesie CIP:
Pierwszym krokiem w wyborze rozwiązań technicznych jest znalezienie wycieków energii. W tym celu można wykorzystać systemy zdalnego monitorowania składające się z czujników i oprogramowania. Czujniki są instalowane na urządzeniach procesowych, a parametry procesu są rejestrowane przez określony czas.
- 85% – ogrzewanie roztworów czyszczących;
- 8% – zużycie wody;
- 6% – praca napędów elektrycznych;
- 1% – sprężone powietrze.
Jak widać, głównym zużyciem są straty ciepła, więc ich analiza jest podstawą do opracowania środków oszczędzania energii.
Na straty ciepła z ogrzewania składają się straty z gorących powierzchni pojemników i rurociągów, z podgrzewanych cieczy, z niewłaściwego doboru parametrów mycia – ogrzewania, czasu, zużycia wody. Są one indywidualne dla każdego zakładu produkcyjnego, ale istnieją podstawowe środki oszczędzania energii, które można zastosować. W każdym przypadku efekt będzie inny.
Izolacja ogrzewanych powierzchni
Straty ciepła są wprost proporcjonalne do różnicy temperatur między ogrzewanymi mediami a otaczającym powietrzem. Rozwiązaniem jest zapobieganie wymianie ciepła między gorącymi powierzchniami a otoczeniem, aby nie uległy one ochłodzeniu.
W tym celu stosuje się izolację urządzeń o temperaturze powyżej 45 °C:
- zbiorniki
- przewody parowe i armatura
- wymienniki ciepła;
- rurociągi.
W naszej praktyce izolacja zbiornika magazynowego rurociągu parowego o pojemności 6 m3 przyniosła około 14 EUR dziennych oszczędności finansowych. Taki zbiornik wymaga 10 płukań dziennie w temperaturze 85°C. Zużycie energii wynosi prawie 510 tys. kcal/dzień.
Izolacja korpusu, dna i pokrywy zbiornika zmniejszyła zużycie ciepła nawet o 230 tys. kcal/dzień. Koszt droższego izolowanego zbiornika magazynowego zwrócił się w ciągu 1,6 roku. Emisja CO2 została zredukowana do 20 ton rocznie. W przypadku zbiorników o pojemności 20 m3 efekt ekologiczny i ekonomiczny będzie jeszcze bardziej zauważalny.
Izolacja termiczna systemów dystrybucji pary zmniejsza zużycie energii o 90%. A jest to ilość bezpośrednich strat z gorących rurociągów. Według naszych szacunków izolacja rurociągów gorącej wody zwraca się w ciągu roku, a rurociągów kondensatu – w ciągu 2 lat. Ponadto zmniejsza się emisja gazów cieplarnianych.
Projekty izolacji gorących powierzchni o temperaturze powyżej 60°C zwracają się w czasie krótszym niż dwa lata.
Zmniejszone straty podczas podgrzewania zaprawy
Ponowne wykorzystanie roztworu czyszczącego i dostosowanie wyposażenia zakładu jest kolejnym skutecznym środkiem oszczędzania energii.
Wiele procesów mycia CIP pozwala na ponowne wykorzystanie płynów, ale nie każda stacja jest do tego przystosowana. Mogą one nie mieć zbiorników odzysku lub linii powrotnych z mytych obiektów.
W rezultacie do każdego mycia konieczne jest podgrzanie nowego roztworu do temperatury 85°C. Zużyty płyn trafia do kanalizacji.
Innym źródłem strat w SIP jest nieprawidłowe ustawienie zaworów ślepych do klap. Największy efekt mycia uzyskuje się, gdy zawory pulsują podczas otwierania i zamykania. Zawory pozostają otwarte przez 5 sekund, co zwiększa przepływ podgrzanego roztworu.
Skrócony czas nagrzewania
Straty energii można zmniejszyć poprzez obniżenie temperatury zbiornika podczas przygotowywania roztworu ługu lub przerw między etapami cyklu mycia.
Na przykład o 10°C. Wymaga to jednak dokładnych obliczeń, aby skompensować różnice temperatur podczas procesu.
Zużycie energii na ogrzewanie zmniejsza się o około 1/60 temperatury o 1 °C. Środek ten pokazuje efekt oszczędzania pary i zasobów w perspektywie długoterminowej.
Wybór parametrów zlewu CIP
Zasada „Analiza i optymalizacja parametrów mycia dla określonych warunków pracy” zawsze działa i prowadzi do oszczędności kosztów.
Proces IP zależy bezpośrednio od trzech elementów:
- mechanicznych – ciśnienia i natężenia przepływu;
- procesu czyszczenia;
- temperatury medium.
Krajowe podejście do oszczędzania energii zakłada zwiększenie komponentu mechanicznego przed czasem czyszczenia i ogrzewaniem. Na przykład, do czyszczenia zbiorników można użyć głowic strumieniowych myjki CIP zamiast głowic szczelinowych. W rurociągach należy zwiększyć turbulencje przy prędkości przepływu co najmniej 1,8 m/s.
Zakres parametrów mycia CIP jest zawsze indywidualny, ponieważ zależy od rodzaju zanieczyszczeń, rodzaju produktu oraz cech konstrukcyjnych sprzętu i rurociągów. Najlepszą opcję dla danej produkcji można wybrać po przeprowadzeniu testów i płukania laboratoryjnego.
Dla. W zakładach przetwórstwa mleka dobry efekt oszczędności energii uzyskuje się poprzez dostosowanie temperatury mycia urządzeń.
Ponowne wykorzystanie wody pitnej
Jest to cenny zasób, ponieważ jego produkcja jest również energochłonna.
Wodę można poddać recyklingowi, aby zaoszczędzić na zużyciu wody pitnej. Ciecz z ostatniego płukania podczas mycia CIP jest używana do pierwszego płukania w następnym cyklu.
Aby wdrożyć to rozwiązanie, konieczna jest modernizacja istniejącego zakładu poprzez instalację urządzeń do odzyskiwania wody: zbiorników i rurociągów.
Zmniejszone straty z pomp
Najskuteczniejszym sposobem ograniczenia strat elektrycznych jest instalacja przetwornic częstotliwości z kontrolą przepływu i ciśnienia.
to urządzenia, które zmieniają częstotliwość prądu przemiennego sieci zasilającej do wymaganych parametrów, co umożliwia dostosowanie prędkości obrotowej silnika pompy zgodnie z potrzebami procesu technologicznego.
Montaż przemiennika częstotliwości to modernizacja instalacji elektrycznej. Projekt i wykonanie tych prac najlepiej powierzyć firmie inżynieryjnej, aby uniknąć skarg ze strony przedsiębiorstwa energetycznego i organów nadzoru energetycznego. Powodem tego jest fakt, że przetwornice częstotliwości mogą pogorszyć jakość energii elektrycznej w głównej sieci.
Utrzymanie właściwego stanu technicznego sprzętu
Sprzęt w złym stanie jest droższy dla właściciela.
Sprzęt w złym stanie jest droższy dla właściciela. Nieszczelne uszczelki, zatkane głowice myjące i zużyte pompy znacznie zwiększają straty pary, wody i energii elektrycznej. Przecieki zmniejszają do zera efekt innych środków oszczędzania energii.
Zamiast tego, terminowa konserwacja, naprawa i wymiana przestarzałego sprzętu jest jednym z warunków racjonalnego zużycia ciepła. Jako przykład weźmy syfony kondensatu.
Jeśli nie były one serwisowane przez 3-5 lat, to około jedna trzecia takiego sprzętu jest w wadliwym stanie, umożliwiając wyciek pary do systemu odwadniającego. Liczby te potwierdza praktyka.
Aby zmniejszyć koszty napraw i wymiany, firmy spożywcze stosują system zdalnego monitorowania. Przemysłowy Internet Rzeczy lub IIoT to odmiana Przemysłowego Internetu Rzeczy. Specjalistyczne czujniki zbierają informacje o parametrach pracy różnych urządzeń i przesyłają je do systemu sterowania. Takie monitorowanie pomaga wydawać pieniądze na naprawę i wymianę niedziałającego sprzętu. Z naszego doświadczenia wynika, że w zakładach przetwórstwa spożywczego z systemem monitorowania nie działa więcej niż 5% syfonów kondensatu, a straty pary są zmniejszone o 10%.
Obecne modele urządzeń są bardziej energooszczędne niż te produkowane kilkadziesiąt lat temu. Na przykład termostatyczne odwadniacze mają obecnie szereg zalet w porównaniu ze starszymi modelami:
- otwierają się, gdy temperatura zbliża się do poziomu pary nasyconej plus lub minus dwa stopnie;
- mogą być używane jako kanały powietrzne;
- emitują nieskroplone gazy po każdym otwarciu;
- skracają czas ogrzewania.
Średni okres zwrotu z wymiany odwadniacza wynosi mniej niż sześć miesięcy.
Zamiast konkluzji
Ma to wpływ na wydajność i zużycie energii przez urządzenia do przetwarzania żywności:
- prawidłowe rozmieszczenie elementów temperatury pary;
- współczynnik przenikania ciepła;
- materiał i typ wymiennika ciepła;
- wydajność wymiennika ciepła;
- obecność nieszczelności.