12.07.2024
Jak
Browary
Jak zmniejszyć zużycie wody w miejscu produkcji piwa
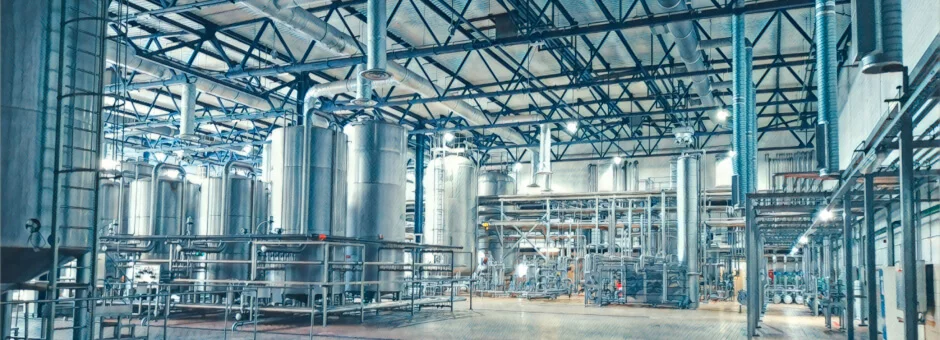
Test szczelności
Wtórne wykorzystanie wody
Modernizacja sprzętu
Kondycjonowanie wody (filtry membranowe, filtry węglowe, filtry wysyłkowe, odwrócona osmoza)
Chłodzenie nachmielonej brzeczki
CIP
Transportery
Węże myjące
Maszyna do mycia butelek
Pasteryzator tunelowy
Płuczka
(maszyna do płukania)
Dodatkowa modernizacja
Klimatyzacja wody
Dobre piwo zaczyna się od wysokiej jakości wody. Piwowar nie może sobie pozwolić na zależność od lokalnych warunków naturalnych, dlatego każdy zakład produkcyjny zawsze posiada stację uzdatniania wody.
Ciecz przechodzi przez kilka etapów:
- zgrubną filtrację mechaniczną, gdzie usuwane są wszystkie nierozpuszczalne zanieczyszczenia do 0,03 mm;
- odfermentowanie;
- wymianę jonową w celu zmiękczenia lub odsolenia.
Liczba etapów uzdatniania wody zależy od składu naturalnych surowców z ujęcia wody, a także od możliwości zakupu sprzętu przez browar. Najczystszą wodę uzyskuje się stosując odwróconą osmozę – separację membranową, która usuwa do 99% wszystkich soli, bakterii i pirogenów.
Straty w miejscu uzdatniania wody stanowią do 30% całkowitego zużycia wody w browarze. Jest to zużycie na okresowe mycie samych filtrów, membran usuwających zanieczyszczenia. Straty surowców w uzdatnianiu wody są tak znaczące, że niektórzy producenci są skłonni zainwestować w wymianę sprzętu, aby ograniczyć marnotrawstwo. Taka sytuacja miała miejsce na przykład u jednego z klientów Viravix Engineering, ale eksperci Viravix zdołali zaproponować mu tańsze procedury.
Jednym z rozwiązań jest odzyskiwanie wody w produkcji. Jest to ponowne wykorzystanie cieczy w procesach technologicznych. Po umyciu filtrów, woda z membran może być zbierana i wykorzystywana do innych celów. Na przykład jest używana do mycia podłóg i ścian.
Jeśli istniejący sprzęt nie pozwala na instalację zbiorników odzysku, zostanie on zmodernizowany. Następnie woda jest zbierana w celu ponownego wykorzystania.
Koszty wody można zmniejszyć, jeśli wyeliminuje się wszystkie wycieki. Jedną z najlepszych praktyk stosowanych przez gigantów piwowarskich jest Dzień Ciszy. Cała produkcja jest zatrzymywana na jeden dzień, a specjaliści szukają wszystkich nieszczelnych miejsc, w których dochodzi do wycieków powietrza, wody i CO 2. Procedura ta może być wykorzystywana do oszczędzania surowców we wszystkich zakładach browarniczych, nie tylko do uzdatniania wody.
Chłodzenie brzeczki chmielem
Optymalizacja zużycia wody w miejscu produkcji piwa nie oznacza bezpośredniej oszczędności zasobów, ale ich rozsądne wykorzystanie.
Firmy spożywcze zawsze muszą zachować równowagę między oszczędnością energii a bezpieczeństwem mikrobiologicznym produktu.
Podczas chłodzenia brzeczki chmielonej powstaje nadmiar gorącej wody. Niektórzy producenci po prostu spuszczają ją do kanalizacji, ponieważ nie posiadają urządzeń chłodniczych na tym etapie. Rozsądni użytkownicy wody instalują pojemniki do zbierania i przechowywania gorącej wody, która może być dalej wykorzystywana w produkcji.
Eksperci inżynieryjni Viravix opracowują zestaw procedur odzyskiwania w produkcji, w oparciu o indywidualne warunki w danym browarze:
- ile gorącej wody pozostaje po schłodzeniu nachmielonej brzeczki;
- jaka jest jakość tego surowca
- ile i jakiej objętości zbiorników można zainstalować;
- do którego procesu łatwiej jest przesłać ciecz – do kotła zaciernego czy do urządzeń prysznicowych.
Jednostki chłodzące zużywają dużo energii elektrycznej i nie wszyscy piwowarzy mogą sobie na nie pozwolić.
CIP
Oszczędność lub redukcja zużycia wody w SIP jest ważnym krokiem w kierunku zrównoważonych i opłacalnych operacji w wielu branżach. W szczególności, stosowanie metody czyszczenia w obiegu zamkniętym (CIP) jest głównym czynnikiem przyczyniającym się do zużycia wody w sektorze produkcyjnym.
W produkcji piwa zawsze istnieje kilka obwodów do mycia sprzętu. Stacje CIP to kolejne miejsce, w którym można zastosować rekuperację w przedsiębiorstwie. Najważniejsze jest, aby zrozumieć, skąd można zbierać roztwór, ile naczyń można umieścić i gdzie można go później wykorzystać.
Viravix Engineering Company zajmuje się projektowaniem, instalacją i wsparciem serwisowym stacji CIP. Początkowo oferujemy klientom procedury oszczędzania energii, ale możemy również pomóc w istniejących stacjach.
Czysta woda podczas czyszczenia CIP jest dostępna przy:
- płukaniu pośrednim – po czyszczeniu roztworem alkalicznym lub kwaśnym;
- płukanie końcowe;
- etap dezynfekcji rurociągów.
Najlepszą opcją redukcji kosztów CIP i wody w przedsiębiorstwie jest rozsądne zużycie i powrót do produkcji.
Jeśli stacja CIP nie jest zaprojektowana do instalacji zbiorników odzysku, można ją najpierw zmodernizować, a następnie zastosować technologię zbierania wody do ponownego wykorzystania.
Inną strategią ograniczania zużycia wody jest jej recykling tam, gdzie jest to możliwe podczas mycia z użyciem środków żrących. Na przykład ponowne wykorzystanie wody płuczącej w procesie CIP lub instalacja systemu odzyskiwania wody w procesie CIP może skutkować zmniejszeniem zużycia wody i związanych z tym kosztów.
Ogólnie rzecz biorąc, zmniejszenie zużycia wody podczas mycia żrącego lub alkalicznego w operacjach CIP jest ważnym krokiem w kierunku zrównoważonych i opłacalnych operacji. Wdrażając strategie mające na celu zmniejszenie zużycia wody, producenci mogą obniżyć koszty wody przy jednoczesnym utrzymaniu wysokiego poziomu czystości i higieny. Dzięki zmniejszeniu kosztów i zużycia wody w procesie SIP, firmy mogą poprawić swoje wyniki finansowe i zmniejszyć swój wpływ na środowisko.
Transportery
Procesy pakowania są znaczącym konsumentem wody w browarnictwie.
Do mycia przenośników i transporterów używa się wielu surowców. Często są one czyszczone ręcznie, przy użyciu węży.
Automatyzacja zmniejsza zużycie, ponieważ eliminuje czynnik ludzki. Dodatkową zaletą czyszczenia maszynowego jest poprawa jakości procesu.
Specjaliści Viravix Engineering zaprojektują, zainstalują i będą serwisować automatyczne myjki do transporterów.
Węże myjące
Są one dostępne w każdym browarze do ręcznego czyszczenia sprzętu, podłóg i ścian.
Aby zmniejszyć zużycie wody, zalecamy stosowanie specjalnych dysz o mniejszej średnicy. Ograniczają one rozpryskiwanie i zwiększają odległość strumienia.
Maszyny do mycia butelek
Są to najbardziej znaczące zużycie wody w procesach pakowania.
Zasada działania maszyny do mycia butelek opiera się na stałym przepływie cieczy przez wanny do:
- mycia wstępnego;
- pierwszego, czasem drugiego mycia alkalicznego
- płukania post-alkalicznego;
- świeżej wody;
- płukanie końcowe.
Zmniejszone zużycie wody w myjce do butelek może również zależeć od konkretnego modelu. Tutaj oferujemy ten sam sposób na zmniejszenie kosztów wody w myjce do butelek – kierowanie surowców w odwrotnej kolejności: od procesów czystych do brudnych. To znaczy, od końcowego płukania do wstępnego odparowywania.
Innym rozwiązaniem zmniejszającym zużycie wody w myjni butelek jest modernizacja strzykawek do płukania butelek. W tym przypadku można kontrolować ciśnienie cieczy: im niższe, tym mniejsze zużycie.
Myjki do butelek posiadają zawór odcinający dopływ wody w przypadku zatrzymania urządzenia. Nie wszyscy piwowarzy zwracają uwagę na jego dobry stan i może on przeciekać. Nie jest to zauważalne, ponieważ obszar wokół maszyny do mycia butelek jest zawsze mokry. Regularne sprawdzanie poprawności działania zaworu odcinającego pozwala również oszczędzać surowce.
Pasteryzator tunelowy
Sprzęt jest używany do pasteryzacji puszek i butelek z piwem. Ponieważ firmy z branży piwowarskiej dążą do bardziej zrównoważonej działalności, nie można przecenić znaczenia technik oszczędzania wody w pasteryzatorze tunelowym. Pojemnik powoli przesuwa się przez tunel i jest pasteryzowany przez 30-40 minut, a następnie chłodzony przez 30-40 minut.
Podczas normalnej pracy linii, ciecz o tej samej temperaturze krąży między wannami w strefie ogrzewania i chłodzenia, a wszystko jest kompensowane. W przypadku zatrzymania linii, aby uniknąć nadmiernej pasteryzacji, gorące wanny są schładzane zimną wodą do temperatury 50°C. Nadmiar płynu jest odprowadzany do kanalizacji.
Dzięki wdrożeniu strategii mających na celu zmniejszenie zużycia wody w pasteryzatorze tunelowym, takich jak instalacja zbiornika odzysku i wymiennika ciepła, firmy mogą czerpać korzyści z bardziej zrównoważonej i opłacalnej eksploatacji.
Koszt takiej modernizacji szacuje się na 15-20 tysięcy euro, ale może się on szybko zwrócić dzięki zmniejszonemu zużyciu wody przez pasteryzator. W dużych pasteryzatorach tunelowych, przy niestabilnej pracy linii, oszczędności sięgają setek metrów sześciennych wody na zmianę.
Co więcej, korzystając z pasteryzatora tunelowego z redukcją zużycia wody, firmy mogą zmniejszyć ogólne zużycie wody i koszty, ponieważ technologia ta wykorzystuje najnowocześniejsze procesy w celu zminimalizowania ilości wody potrzebnej do procesu pasteryzacji.
Jeśli w istniejących pasteryzatorach nie można zainstalować zbiorników odzysku, modernizacja sprzętu jest kolejną opcją zmniejszenia zużycia wody w pasteryzatorze tunelowym, dzięki czemu firma może czerpać korzyści z bardziej zrównoważonej i opłacalnej działalności.
Rinser
Na wszystkich liniach PET, liniach puszek i tam, gdzie używane są nowe szklane butelki, zainstalowane są płuczki.
Płuczki mogą być również wyposażone w zbiorniki odzysku. Początkowo producenci sprzętu oferują tę opcję, ale nie wszyscy piwowarzy rozumieją jej cel i odmawiają takich wydatków.
Tymczasem ponowne wykorzystanie wody z płuczki znacznie zmniejsza jej zużycie. Nie oznacza to, że browar będzie w stanie całkowicie zrezygnować z używania świeżej wody. Ale odnawianie wody w płuczce stanie się rzadsze.
Dodatkowa aktualizacja
Specjaliści Viravix Engineering mogą zaoferować inne rozwiązania w celu zmniejszenia zużycia wody w browarze. Wszystko zależy od konkretnych warunków produkcji.
Gdzieniegdzie możliwe jest wykorzystanie wody drenażowej z oczyszczalni ścieków; gdzieniegdzie – zainstalowanie pojemników do zbierania wody deszczowej.
Konkretna lista procedur oszczędzania energii jest ustalana na miejscu. Powtarzamy, że w warzeniu piwa ważne jest znalezienie równowagi między oszczędnością surowców a jakością piwa.