16.07.2024
Как
Как сократить потребление электроэнергии на пищевом производстве
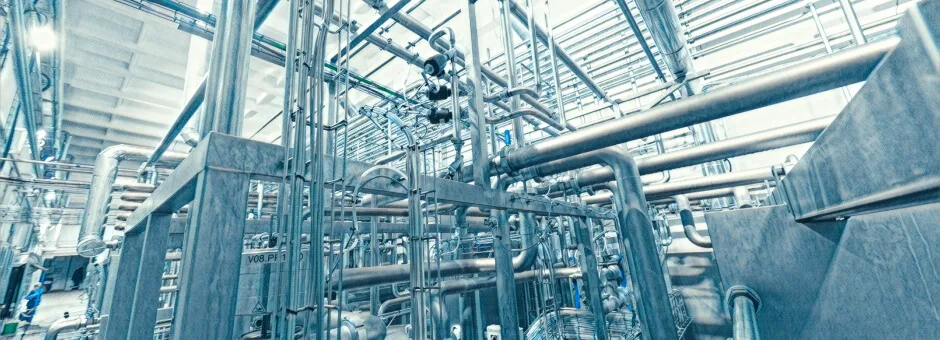
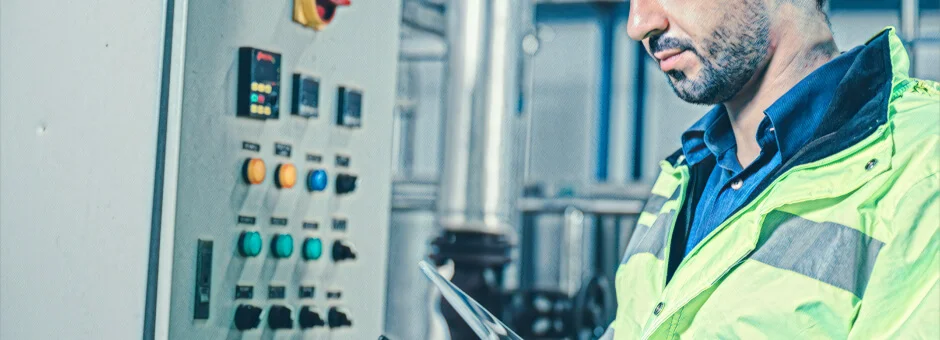
Структура основных энергозатрат на производстве
Почти половина энергопотребления пищевого производства, например, переработки молока, приходится на процессы очистки технологического оборудования и трубопроводов. Но отказаться от СИП-мойки нельзя, поскольку без нее не обеспечивается необходимая бактериологическая чистота продукта.
В статье СИП-мойка на пищевых производствах мы уже описали, какие ошибки можно допустить при внедрении оборудования и как их избежать.
Если установить СИП станцию без понятного руководства по эксплуатации или с неправильным монтажом, это может привести к серьезным проблемам, включая гидроудары, поломки и невозможность проведения полноценного технического обслуживания.
Инженер-технолог, который сталкивается с авариями, разбрызгиванием моющего раствора и конфликтами в графике мойки различного оборудования, не оценит преимущества автоматизации, поскольку ему придется лично контролировать весь процесс.
Если мойка устанавливается без учета условий производства, это может повлечь проблемы и для специалиста по качеству, который может столкнуться с наличием «мертвых зон» на линии и невозможностью отбора проб. Чтобы избежать таких проблем, необходимо обратиться к надежной инжиниринговой компании, которая поможет подобрать оборудование и обеспечит правильный монтаж.
Владелец пищевого производства сможет сэкономить больше на минимизации рисков, чем заплатит за услуги такой компании.
Ориентировочная структура энергозатрат при CIP-процессе:
Первый шаг в подборе технических решений — найти утечки энергии. Для этого можно использовать системы удаленного мониторинга, состоящие из детекторов и программного обеспечения. На технологическое оборудование устанавливаются датчики, и в течение определенного периода записываются параметры технологического процесса.
- 85 % — нагрев моющих растворов;
- 8 % — использование воды;
- 6 % — работа электрических приводов;
- 1 % — на сжатый воздух.
Как видно, основной расход приходится на тепловые потери, поэтому их анализ первичен для разработки мероприятий по энергосбережению.
Тепловые потери от нагрева состоят из потерь от горячих поверхностей емкостей и трубопроводов, от нагретых жидкостей, от неправильного выбора параметров мойки — нагрева, времени, расхода воды. На каждом производстве они индивидуальны, но есть основные меры по энергосбережению, которые можно применить. Просто эффект в каждом случае будет разный.
Изоляция нагретых поверхностей
Теплопотери прямо пропорциональны разнице температур нагретых сред и окружающего воздуха. Выход — не допускать теплообмена между горячими поверхностями и окружающей средой, чтобы не было их охлаждения.
Для этого применяется изоляция оборудования с температурой выше 45 °С:
- емкостей;
- паропроводов и арматуры;
- теплообменников;
- трубопроводов.
В нашей практике изоляция бака-накопителя паропровода объемом 6 м3 приносила около 14 евро ежедневной финансовой экономии. Для такой емкости требуется 10 промывок в день при температуре 85 °С. Потребление энергии при этом составляет почти 510 тыс. ккал/сутки.
Изоляция корпуса, дна и крышки емкости позволила сократить расход тепла до 230 тыс. ккал/сутки. Затраты на более дорогой изолированный бак-накопитель окупились за 1,6 года. А выбросы СО2 сократились до 20 тонн в год. На резервуарах 20 м3 экологический и экономический эффект будет еще заметнее.
Теплоизоляция систем распределения пара дает сокращение энергопотребления на 90 %. И это объем прямых потерь от горячих трубопроводов. По нашим подсчетам, теплоизоляция магистралей для горячей воды окупается за год; труб конденсата — за 2 года. Дополнительно сокращаются выбросы парниковых газов.
Проекты теплоизоляции горячих поверхностей от 60 °С окупаются меньше, чем за два года.
Сокращение потерь при нагревании раствора
Повторное использование моющего раствора и настройка оборудования станции — еще одно результативное мероприятие по энергосбережению.
Во многих процессах СИП-мойки допускается повторно использовать жидкости, но не всякая станция оборудована для этих целей. В ней могут отсутствовать емкости для рекуперации и возвратные магистрали от объектов мойки.
В результате для каждой очистки нужно нагревать новый раствор до 85 °С. А использованная жидкость уходит в дренаж.
Еще один источник потерь в СИП — неправильная настройка тупиковых клапанов на флиппирование. Наибольший эффект от мойки достигается при их пульсации в момент открывания-закрывания. А клапаны оставляют открытыми на 5 секунд, что увеличивает расход нагретого раствора.
Сокращение времени нагревания
Потери энергии можно сократить, снизив температуру емкости на время приготовления щелочного раствора или пауз между этапами цикла мойки.
Например, на 10 °С. Но здесь нужен точный расчет, чтобы компенсировать разницу температур во время технологического процесса.
Расход энергии на нагрев при снижении на 1 °С уменьшается примерно на 1/60. Такая мера показывает эффект экономии пара и ресурсов в долгосрочной перспективе.
Выбор параметров СИП-мойки
Принцип «Анализ и оптимизация параметров мойки под конкретные условия эксплуатации» работает всегда и приводит к сокращению затрат.
СИП-процесс прямо зависит от трёх составляющих:
- механической — давления и скорости потока;
- времени очистки;
- температуры сред.
Рациональный энергосберегающий подход подразумевает увеличение механической составляющей перед временем мойки и нагревом. Например, для очистки ёмкостей и резервуаров можно использовать струйные головки СИП-мойки вместо щелевых. В трубопроводах увеличивать турбулентность со скоростью потока не менее 1,8 м/сек.
Выбор параметров СИП-мойки всегда индивидуален, поскольку он зависит от типа загрязнений, вида продукта, конструктивных особенностей оборудования и трубопроводов. Найти наилучший вариант для вашего производства можно после проведения тестов и лабораторных смывов.
Пример. На предприятиях переработки молока хороший энергосберегающий эффект даёт подбор температуры очистки оборудования.
Повторное использование питьевой воды
Это ценный ресурс, поскольку его производство также энергозатратное.
Бережно расходовать питьевую воду можно при помощи её повторного использования. Так жидкость от последнего ополаскивания при СИП-мойке применяют для первой промывки в следующем цикле.
Для того, чтобы это реализовать, нужна модернизация существующей станции с установкой рекуперационного оборудования: ёмкостей и трубопроводов.
Сокращение потерь от насосов
Наиболее эффективной мерой снижения электрических потерь является установка частотных преобразователей с контролем расхода и давления.а относится к модернизации электроустановки.
Это устройства, которые меняют частоту переменного тока основной сети до нужных параметров, что позволяет регулировать скорость электродвигателя насоса в соответствии с потребностями технологического процесса.
Установка частотника относится к модернизации электроустановки. Проектирование и выполнение этой работы лучше поручить инжиниринговой фирме, чтобы не получать претензии от сетевой компании и органов энергонадзора. Дело в том, что частотные преобразователи могут ухудшать качество электроэнергии в основной сети.
Обслуживание и поддержание технического состояния оборудования
Оборудование в плохом состоянии обходится владельцу дороже.
Негерметичные уплотнения, забитые моющие головки и изношенные насосы сильно увеличивают потери пара, воды, электричества. Протечки сведут «на ноль» эффект от реализации других энергосберегающих мероприятий.
Поэтому своевременное техническое обслуживание, ремонт и замена устаревшего оборудования — одно из условий рационального теплопотребления. Приведём в пример конденсатоотводчики.
Если их техобслуживание не проводилось 3-5 лет, то около трети такого оборудования находится в неисправном состоянии, позволяя пару просачиваться в систему отвода. Такие показатели подтверждаются практикой.
Чтобы сократить затраты на ремонт и замену, пищевые предприятия применяют систему удаленного мониторинга. Это вариация промышленного интернета вещей — Industrial Internet of Things или IIoT. Специальные датчики собирают информацию о параметрах работы разного оборудования и передают их в систему управления. Такой мониторинг помогает тратить средства на ремонт и замену именно неработающего оборудования. По нашему опыту на пищевых предприятиях с системой мониторинга неисправно не более 5 % конденсатоотводчиков, а потери пара уменьшаются на 10 %.
Современные модели оборудования более энергоэффективны, чем выпущенные десятки лет назад. Например, сейчас термостатические конденсатоотводчики имеют ряд преимуществ перед старыми моделями:
- они открываются, когда температура приближается к уровню насыщенного пара плюс-минус два градуса;
- могут использоваться как воздухоотводы;
- выбрасывают неконденсирующиеся газы после каждого открытия;
- уменьшают время на нагрев.
Средний срок окупаемости замены конденсатоотводчика составляет менее шести месяцев.
Вместо заключения
На эффективность работы и энергопотребление пищевого оборудования влияют:
- правильное расположение элементов паровой температуры;
- коэффициент теплопередачи;
- материал и тип теплообменника;
- производительность теплообменника;
- наличие утечек.