17.05.2024
Turnkey
Confectionery
Turnkey sugar syrup station
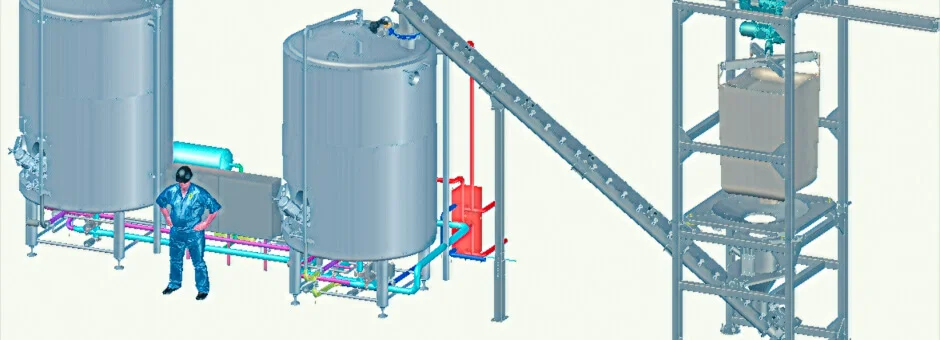
We installed a sugar syrup station with a total capacity of 4 tonnes/hour. The project was carried out on a turnkey basis, from concept design to commissioning and integration into a DCS. The implementation period was 2020-2021.
Client
Our client is a large brewery in Ukraine. Due to the terms of the confidentiality agreement, we do not disclose its location and name.
Problem
The client planned to expand the product range with new beers and low alcohol beverages that required a sweet syrup 67 Brix. The raw material used was crystalline sugar in 1,000 kg big-bags.
Mechanical preparation of the syrup using manual labour has its own risks:
- Incorrect sugar dosage, which leads to a recipe failure and deterioration in the quality of the final product.
- Microbiological contamination during manual operations.
- Unsafe working conditions. Sugar can form a flammable, explosive mixture of icing sugar and air when transported and unloaded. Also, manual handling of loose products, which are prone to dust formation, contributes to the development of occupational diseases in workers. And one of the employer’s responsibilities is to ensure a safe working environment.
The customer wanted an automated sugar syrup line to ensure the right concentration of sugar, avoid contamination of drinks and minimise human error.
Tasks
- To design, install and commission an automated crystal sugar syrup station with a concentration of 67 Brix and a capacity of 4 tonnes/hour.
- Provide UV treatment for dosing the glaze into the filtration line.
- To integrate the syrup cooking station into the existing SCADA Montelectro at the plant with the debugging of all processes: production and storage of the product, CIP washing of the equipment.
Reference. 67 Brix stands for 67% sucrose content in water. SCADA is a program for the automated control of the brewery.
Technical solutions
During the preparatory phase, Viraviks Engineering’s engineers gathered initial data for the design of the plant at the customer’s site. We had to “fit” the new facility into the existing production facility, taking into account the existing operational constraints.
Viravix Engineering’s experts completely designed the sugar syrup station:
- made a P&ID drawing – a process flow diagram showing the main and auxiliary elements, the links between them and the control units;
- prepared a 3D model of the future station to visualise the layout solutions;
- drawing up a bill of quantities for equipment and accessories in accordance with the customer’s requirements.
The installation of the station was carried out jointly with the brewery staff. Such approach reduced the cost of the project and minimized the risk of incorrect installation. All work was carried out under the continuous supervision of Viraviks experts, and prior to installation we trained the client’s staff.
Together with the brewery’s staff we have carried out the connection of the station to the utilities SCADA Montelectro, tested the operation of the equipment. Our programmers fine-tuned the automation software solutions during pilot operation.
Information. Equipment and software from brands used in the project:
- shut-off valves – GEA, Burkert;
- sensors – Anton Paar, Endress Hauser, IFM;
- pump – GEA;
- Capacity equipment – Orion.Group;
- wiring and integration – LLC ELAKS.
Viravix officially cooperates with some of the manufacturers from the list, so we can offer our customers a 15-20% discount on components as an engineering company.
Result
The client was supplied with an automated crystal sugar syrup station with a concentration of 67 Brix and a capacity of 4 tons / hour. The equipment was integrated into the company’s existing SCADA control system Montelectro.
The tests showed that the plant met the customer’s requirements in terms of throughput, degree of automation and microbiological purity of the product.