04.08.2024
Study
North American stainless steel
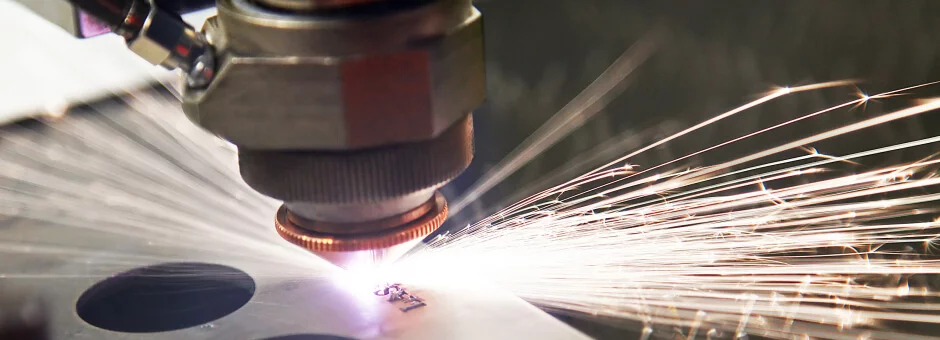
We offer information on 316 and 316L SS, which are molybdenum-containing austenitic stainless steels. These steels contain more nickel than 304SS and 2 to 3% molybdenum. This composition gives these steels increased corrosion resistance in many aggressive environments and resistance to pitting. The addition of molybdenum provides greater resistance to pitting and crevice corrosion in environments containing chlorides, seawater, and chemical environments such as sulfuric acid, phosphoric acid, and acetic acid compounds. The low rate of general corrosion in mildly corrosive environments gives the steel good resistance to atmospheric corrosion in polluted marine environments.
316 SS provides good strength and creep resistance, as well as excellent mechanical properties and corrosion resistance at sub-zero temperatures. 316L is a low-carbon modification of 316. Controlling the carbon content to 0.03% minimizes the problem of carbide precipitation during welding and allows the steel to be used in the welded state in a wide range of corrosion applications.
Standard chemical composition
Nominal mechanical properties (annealed state)
PROPERTIES AT HIGH TEMPERATURES
SHORT-TERM TENSILE PROPERTIES AT ELEVATED TEMPERATURES
MAXIMUM RECOMMENDED OPERATING TEMPERATURE
(UNDER OXIDIZING CONDITIONS)
REPRESENTATIVE TENSILE AND TEAR PROPERTIES
THE PROPERTIES LISTED BELOW ARE SPECIFIC TO FIRED CS316 ONLY
PHYSICAL PROPERTIES
The values below are for 20°C, unless otherwise stated
CONSIDERATIONS FOR FATIGUE
When considering the fatigue of austenitic stainless steels, it is important to note that design and workmanship, rather than material, are the primary factors affecting fatigue failure. Design standards (e.g., AS M E) use data from low-cycle fatigue tests performed on machined specimens to derive conservative S-N curves with stress concentration factors (k1c) or fatigue strength reduction factors (kt). In essence, the fatigue strength of a welded joint must be used for design purposes, as unavoidable defects (even just cross-sectional changes) in the weld will control the overall fatigue performance of the structure.
ANNEALING
Annealing of Types 316 and 316L is achieved by heating to temperatures in excess of 1900°F for approx. 60 minutes per inch of thickness, followed by water or air quenching. The best corrosion resistance is achieved when the final annealing temperature is 1950°F. A controlled atmosphere is recommended to avoid excessive surface oxidation. Temperatures above 1975°F are not recommended unless the wire is annealed in a controlled atmosphere.
STRESS RELIEF
HOT JOB
316 is easy to forge, deform and hot work. Uniform heating of steel in the range of 2100°F to 2300°F is required. The final temperature should not be lower than 1650°F. Crimping and forging operations require a finishing temperature in the range of 1700 to 1800°F. The forgings should then be cooled in air. After all hot working operations, annealing, pickling and passivation should be performed to restore mechanical properties and corrosion resistance.
COLD WORKSHOP
SOFTNESS
As with all austenitic steels, this group of steels produces coarse and tough chips. To prevent chipping, tools with rigid support and as long a cutting edge as possible should be used. Viravix Engineering offers 316L low alloy steel suitable for machining.
A HOUSE ON THE LAND
Types 316/316L have good welding characteristics and are suitable for all standard welding methods. Filler wire should be used either the same or lightly alloyed (e.g. ER W 309 M o). To ensure maximum corrosion resistance, ordinary 316 steel should be annealed after welding to dissolve any chromium carbides that may have precipitated. Discoloration of the weld should be removed by pickling and passivation to restore maximum corrosion resistance.
STRESS CORROSION CRACKING
Stress corrosion cracking (SCC) can occur in austenitic stainless steels when they are energized in a chloride environment at temperatures above 140°F. The stress may be applied, as in pressurized systems, or it may be residual stress resulting from cold working or welding operations. In addition, the chloride ion concentration must not be too high initially if there are areas where salt concentrations can build up. Therefore, estimating these parameters and accurately predicting the probability of SCC during operation is a challenging task.
Where SCC is likely to occur, it is easy to increase the service life by reducing the operating voltage and temperature. As an alternative, specially developed duplex steel 2205 should be used.
IN CASE OF SPHERICAL CORROSION
The atmospheric corrosion resistance of austenitic stainless steel is unmatched by virtually any other uncoated structural material. Stainless steel develops maximum resistance to staining and pitting when molybdenum is added. For this reason, these grades are commonly used in areas where the atmosphere is heavily polluted with chlorides, sulfur compounds and particulate matter, either alone or in combination with other substances.
INTERCRYSTALLINE CORROSION
Sensitization can occur when the weld zones of some austenitic stainless steels that have been heat-affected are cooled in the temperature range of 850° to 1550°F. At these temperatures, positional changes can occur at the grain boundaries. If the sensitized material is then exposed to a corrosive environment, intergranular attack can occur. This corrosion occurs mainly in the heat affected zone at a distance from and parallel to the weld. The susceptibility to this form of attack is often referred to as “weld disintegration”.
316SS has sufficient resistance to carbide precipitation. However, 316L steel should be used for welded structures unless higher carbon steel types are required to increase strength.
RESISTANCE TO CORROSION
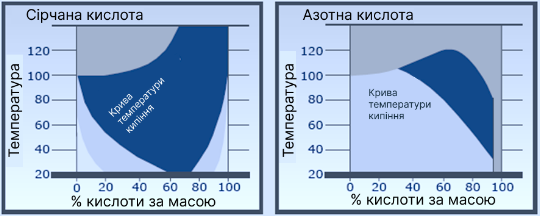
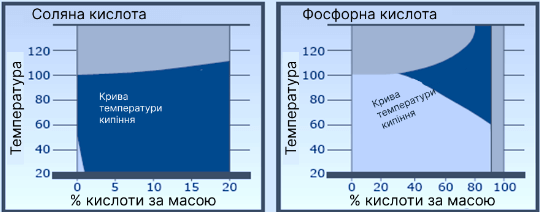
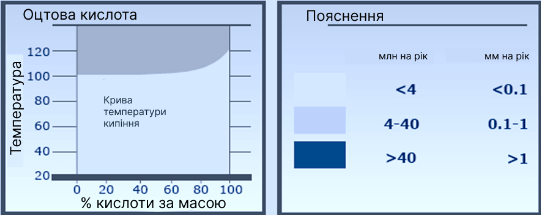
PITTING CORROSION
Corrosion resistance is important mainly for applications involving contact with chloride solutions, especially in the presence of oxidizing environments. These conditions can promote localized penetration of the passive surface film onto the steel, and a single deep corrosion crack can be more damaging than a much larger number of relatively shallow corrosion cracks. The addition of molybdenum to the steel ensures that 316SS has good resistance to localized corrosion such as pitting and crevice corrosion. The diagram below shows the critical pitting temperature (CPT) at different chloride contents for 304, 316 and 2205 steels.
OXIDATION
316/316L SS steel has good oxidation resistance in batch service up to 1600°F and in continuous service up to 1700°F. Continuous use of type 316SS in the temperature range from 850° to 1550°F is not recommended due to the possibility of carbide precipitation, but they work well at temperatures fluctuating above and below this range. In these cases, 316L steel should be used.